The 8 Different Types of Loading Docks
In today’s commercial workplace, facilities must ensure that their loading dock areas are efficient and safe. Ensuring that the loading dock is appropriately designed and that dock equipment is adequately suited for the loading process and unloading can not only improve efficiency but also could prevent costly accidents and worker injuries down the road.
The dock area is a vital hub of activity in many facilities, whether it is a factory, warehouse, plant, or other commercial space. Inefficient loading dock design, processes, and equipment can be very costly for the company. Proper dock design can improve essential loading dock area functions and enhance worker safety.
Some safety problems can be attributed to the initial design of the dock area. Some designs do not take into consideration the expansion of manufacturing and production or how the dock may be utilized in the future. Examples of poor dock design can include poorly-planned approaches, doorways that are too small, improper bumper projections, excessive slopes, gravel approaches, and docks that are not high enough to accommodate the height of a trailer.
Crucial steps can be taken to prevent large remodeling expenses in the future. Whether the dock is built to standard height or proper equipment is used will influence how companies will do business, not to mention saving money and time.
The loading dock area can have many variations to it. Any drawings or specs related to designing a dock should be developed by experienced professionals, such as architects and loading dock personnel. It is necessary to follow state guidelines and local compliance codes when incorporating loading dock designs.
The most common types of loading docks include the following:
Enclosed Loading Dock

Enclosed docks are generally used when product protection, climate control, security and overhead lift capabilities are needed. This type of design is frequently used by package handlers with box truck fleets since it improves efficiency and comfort while decreasing the chance of theft. This design also allows space for overhead cranes that will efficiently load and unload flat-bed trucks. The covering also allows for the placement of overhead dock lights.
An enclosed dock is also the most expensive loading dock design since it requires initial investment and maintenance. Safety concerns for this type of dock include the need for proper ventilation and air-exchange because of truck exhaust fumes that occur inside the building because of the trucks that park indoors.
All your loading dock equipment will be much more protected than if you were using open loading docks. Being able to have the entire truck park inside may be attractive to some truck drivers that need to work in your loading area.
Flush Loading Dock

Flush docks are the most common type of loading dock. A flush dock, which is flush with the outside wall of the building and shares the same foundation, offers a seamless and space-efficient loading solution for warehouses and distribution centers. This design ensures that goods can be loaded and unloaded directly from the building’s interior. Moreover, modern warehouse management systems often incorporate technology like QR codes to streamline inventory tracking and management, enhancing the efficiency of these loading docks even further.
Some safety considerations for flush docks include ensuring that the building wall goes past the foundation (due to the use of metal or other materials) and dock bumper protection. With this type of dock, bumpers should have a minimum of 4.5” feet from the wall, and the wall should project at least one foot past the foundation where the bumpers are mounted.
The loading dock door and dock equipment in a flush dock are exposed to the weather. Having a good door seal to provide weather protection is important. If you have more extreme temperatures or weather dock shelters may be a better fit for you.
Open Loading Dock

Open docks are not usually recommended or used due to exposure to outside weather and the possibility of making it easier for theft to occur. Open loading docks often cannot be heated or cooled efficiently, and they do not provide adequate protection for product, materials or workers. Proper floor drainage is also a consideration due to weather exposure. Edge markings, run-off protection, and handrails may be required as per OSHA standards for an open loading dock.
Open loading docks should always have a canopy. If the canopies are planned over docks that are on sloped driveway grades, the canopy height must be calculated to accommodate trailer height.
Sawtooth Loading Dock

Sawtooth docks present a solution to design situations where the apron space is limited. Sawtooth docks line-ups are used when there is limited outdoor maneuvering space to maneuver trucks. However, the oncoming roads should be designed in a way that trailers and trucks leave in the direction of the angle of the dock. The trucks will require less space to move around because they are already lined up in the direction of the driveway. This is a boon to commercial facilities with limited space that need to save space in their loading area to increase warehouse space.
However, sawtooth loading docks reduce the use of dock space, which makes it more difficult to move and store incoming products, because the staging area between docks in most warehouses is typically not useable.
Cantilever Docks
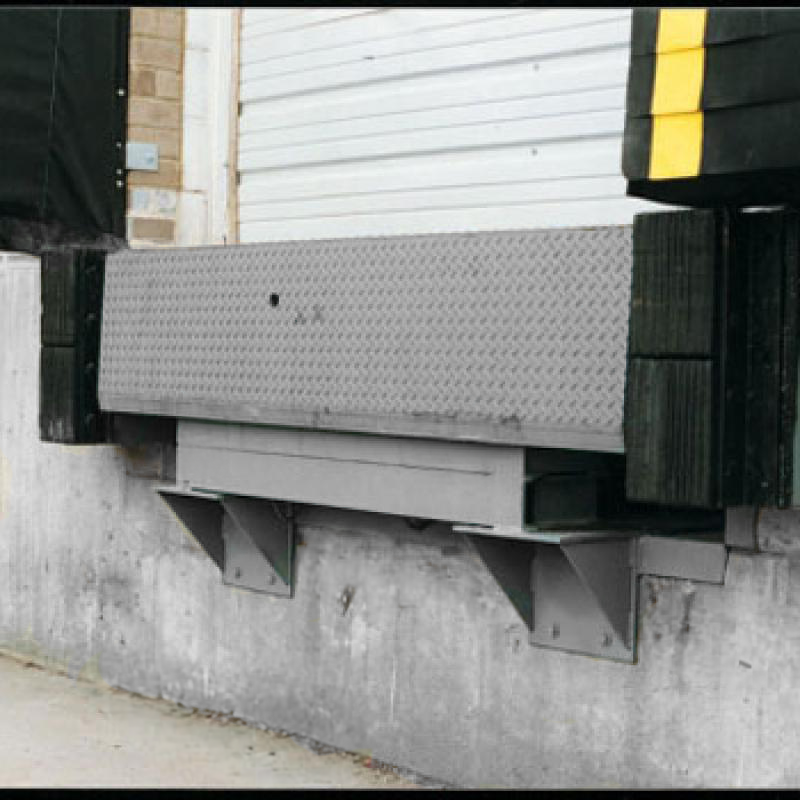
Cantilever docks are similar to flush docks, but they have a cantilevered platform that extends out from the side of the building. This allows forklifts and other loading equipment to drive directly onto the dock and provides a place for them to securely park while they are not in use. Cantilever docks can be more efficient than flush and open docks, but they can also be more expensive.
Drive-In Dock

Drive-in docks, also referred to as drive-through docks, are characterized by their unique design, allowing vehicles to drive directly into the warehouse or facility for loading and unloading operations. They feature openings on both ends, enabling vehicles to enter from one side and exit from the other. Drive-in docks are particularly useful in scenarios where quick turnaround times are essential, as they eliminate the need for turning around or maneuvering within the dock area. They are commonly employed in industries with high-volume operations or time-sensitive deliveries.
Declining or Inclining Loading Dock
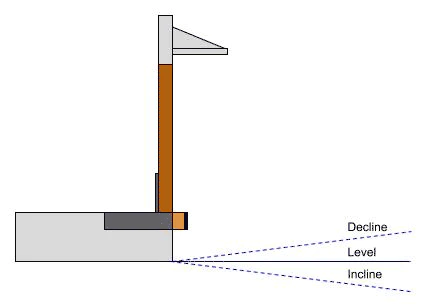
When the building or facility does have basements or dock-level floors, then declining loading docks with slope driveways are often used. Incoming trucks are backed into position at an angle determined by the percentage of the decline of the driveway.
When designing a declining loading dock, the grade of the driveway should not exceed 10%. This design prevents the top of the truck from hitting the ceiling of the building causing structural damage, stops loads of cargo from toppling out, and eliminates traction problems due to snowy or icy conditions.
Another method of design for a decline loading dock is to move the dock leveler pit forward. The amount of projection is determined by the grade of the driveway decline. Projecting the dock leveler pit at the onset can reduce damage caused by vehicle impact to the building, as well as the need for bumper extensions or longer hinged lip assemblies. You will find the same is true on an incline as well. Except, instead of the top of the truck, it’s the bottom of the ICC (aka Jane Mansfield) bar that could hit and damage the face of the loading dock.
If the decline or incline of a loading dock is severe, cargo may fall out, unloading and loading boxes can be tricky, and higher wear and tear will be placed on any equipment that is used for product handling.
Elevated Dock
Elevated docks, also known as high-level docks, are positioned at an elevated level, typically above ground or dock level. These docks are designed to accommodate trucks or trailers with varying bed heights, as they can be adjusted to match the vehicle's height using dock levelers or dock plates. Elevated docks offer the advantage of improved access and compatibility with different types of vehicles. They are commonly found in logistics hubs, distribution centers, and facilities dealing with a wide range of cargo and vehicles.
Dock Management
As your business grows, doing things by hand or using Excel will probably
not be enough. You should consider checking out software tools that will
help manage your warehouse. Our friends over at GoRamp, who make supply
chain software, created a great guide to warehouse management software.
PartsBrite.com specializes in providing the highest-quality aftermarket loading dock parts. We provide companies with warehouse loading docks the parts designed to meet your specific needs. Our sales office is in Southern California, but we ship from warehouses in California and Wisconsin to provide parts to companies located throughout the United States. Contact us at 1-855-PARTSBRITE (1-855-727-8727).
Owner, Parts Brite
My background is in Electrical and Software Engineering, but since I started PartsBrite.com in 2016, I've focused on everything related to docks.
My team and I are here to help those looking to repair or replace their dock levelers, bumpers, door, and door lights.
1-855-PartsBrite | partsbrite.com | paul@partsbrite.com
Leave a comment