Understanding the 4 Key Differences: What is the Difference Between a Loading Bay and Dock?
In the realm of logistics, understanding “what is the difference between a loading bay and dock” is fundamental. A loading dock is an elevated platform designed to align with vehicle beds for streamlined loading, while a loading bay is generally a wider area that may vary in its relation to vehicle height and is used for an assortment of loading tasks. This piece succinctly explains these differences and their practical implications in logistics.
To delve a bit deeper, one could compare a loading dock to a dedicated charging station for electric vehicles – it's specifically designed for one purpose and equipped with all the necessary connections for efficiency and safety. In contrast, a loading bay can be likened to a parking lot that can accommodate various types of vehicles, not just electric ones, and offers the flexibility to handle different activities, such as sorting, temporary storage, and even repackaging operations, in addition to loading and unloading.
Understanding these nuances is crucial for warehouse design, equipment selection, and process optimization, ensuring that the flow of goods is managed effectively and safely.
Key Takeaways
-
Loading docks are specialized, elevated platforms that facilitate direct truck access for efficient loading and unloading, while loading bays are broader areas that can vary in design to accommodate different sizes of vehicles and are not necessarily elevated.
-
Operational efficiency, adaptability, and safety features such as dock levelers and vehicle restraints distinguish loading docks from loading bays, with docks being more suited for high-volume warehouses and bays providing flexible solutions for various warehouse activities.
-
There are specific advantages and disadvantages to each option; loading docks enhance the flow of goods and security but may pose safety challenges, whereas loading bays offer adaptability and cost savings but may lack specialized equipment which can affect efficiency.
Loading Docks vs. Loading Bays: Defining the Terms
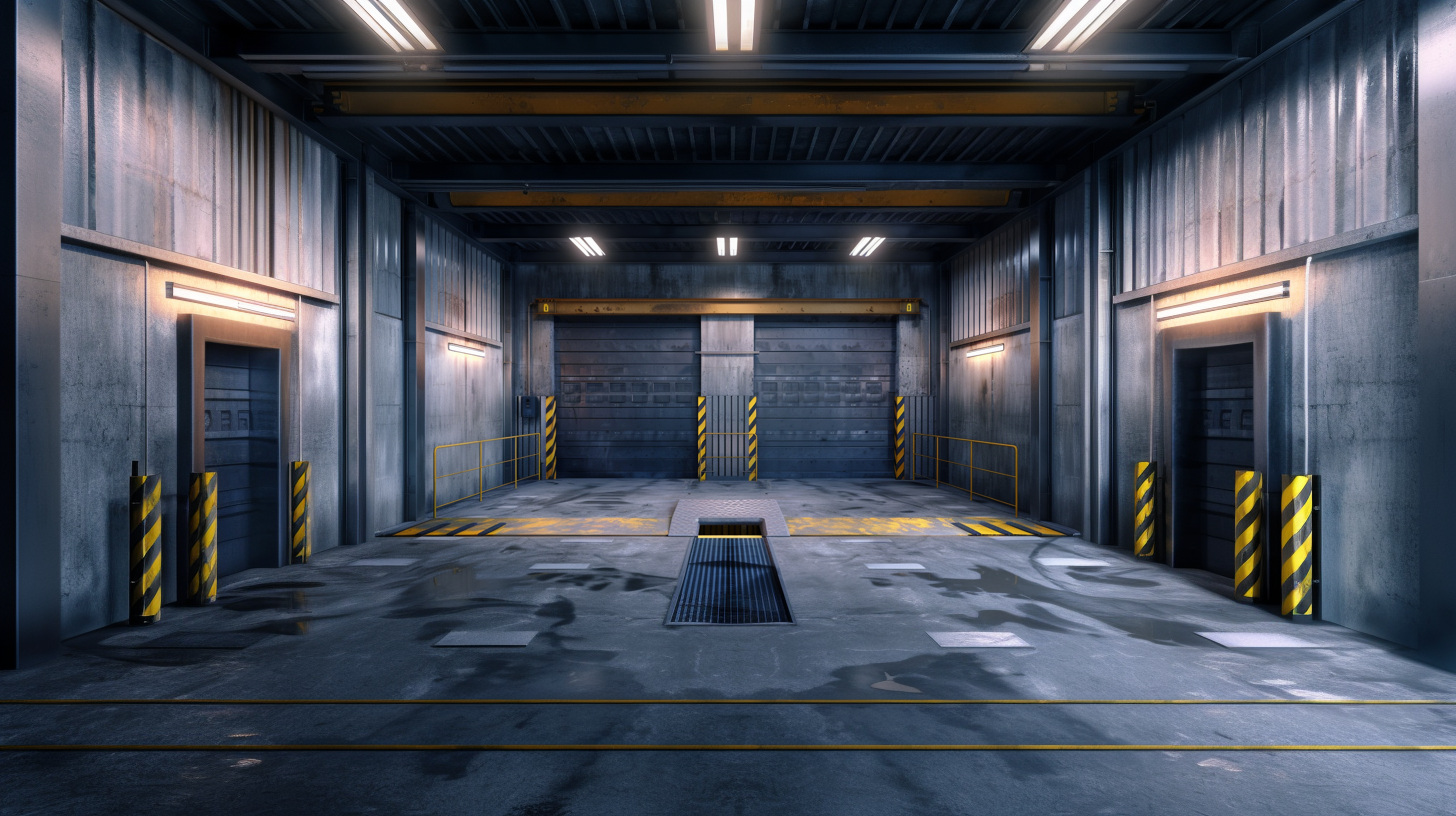
Typically, a loading dock is an elevated platform designed for alignment with transport vehicle beds, thereby facilitating easy access for loading and unloading operations. On the other hand, a loading bay isn’t necessarily elevated to match the vehicle bed height and can encompass a range of areas for loading activities.
The distinction is akin to comparing a specialized tool to a Swiss Army knife; the loading dock is like a dedicated wrench, perfectly crafted for a specific bolt, while the loading bay is more of a multi-tool, capable of performing a variety of functions with its different components.
This versatility is particularly advantageous in scenarios where the logistics operations need to be adaptable to different types of cargo and methods of transportation. For businesses that handle a diverse range of products or have varying shipment sizes, the flexibility of a loading bay can be a significant asset.
Moreover, the design and layout of loading bays can be tailored to meet the specific requirements of the facility, whether it involves direct vehicle-to-warehouse access or includes additional space for staging and sorting goods before they are stored or shipped. This can lead to more efficient use of space and resources, as the area can be configured to optimize the flow of goods and accommodate the necessary equipment, such as forklifts and pallet jacks.
In contrast, the loading dock's specialized design is optimized for quick and safe transfer of goods directly from trucks to the warehouse. This design often includes features such as dock levelers, which adjust the height of the dock to match the truck bed, and dock seals or shelters, which help maintain temperature control and protect goods from the elements during the loading process.
In essence, while loading docks refer to raised platforms specifically for truck access, loading bays represent a broader category inclusive of various configurations for loading activities.
Loading Dock
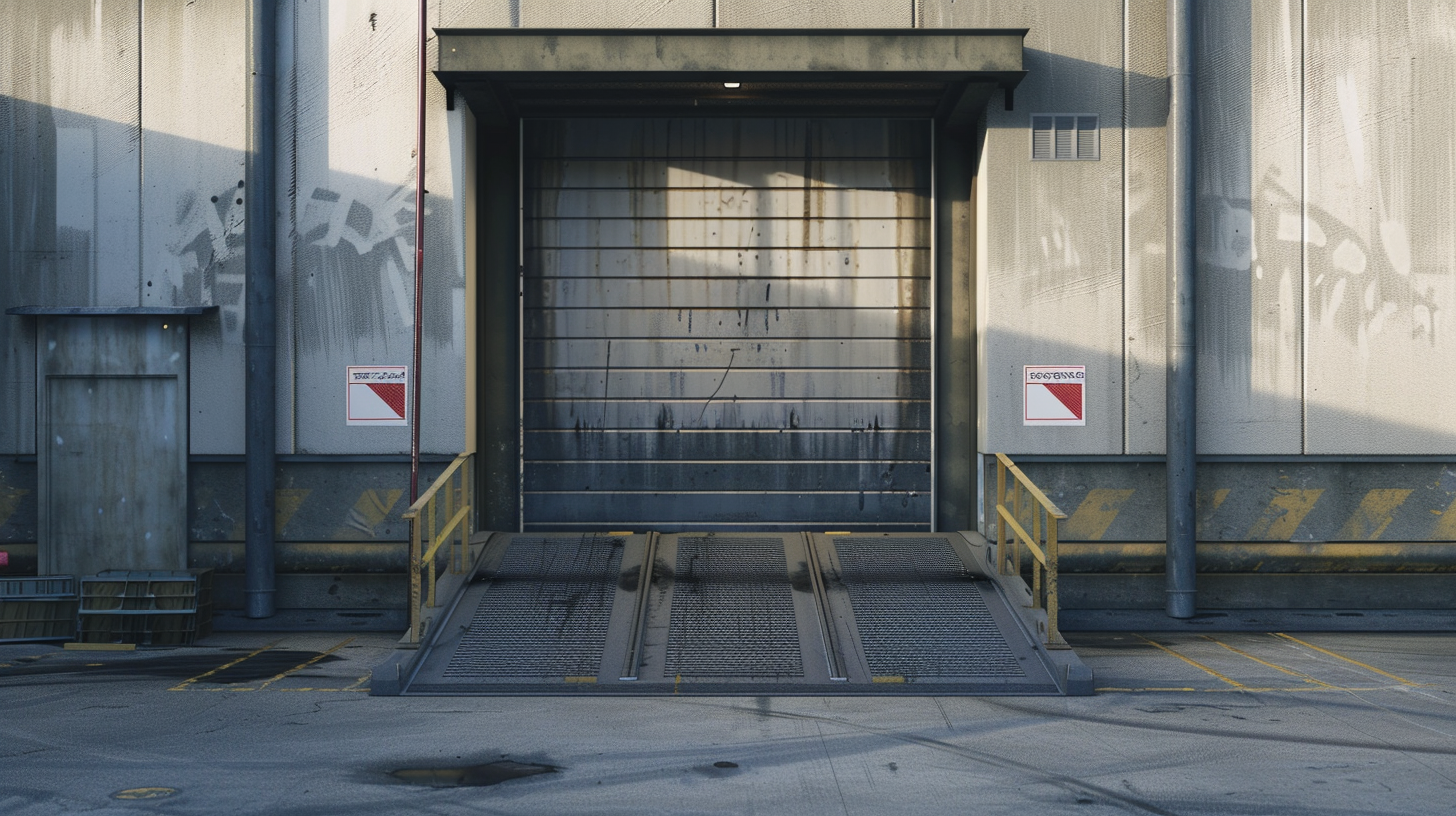
Take a stroll through any warehouse, and you’re bound to come across a loading dock. It serves as a vital junction, an entrance, or exit point for goods in the loading dock area. Picture a platform wide enough to accommodate a majority of trucks, tailored to the height of the most frequent vehicle, and equipped with shock-absorbing bumpers. That’s your quintessential loading dock.
But that’s not all. A loading dock is much more than a raised platform. It’s an intricate system furnished with various components, including:
-
Dock levelers to bridge gaps between the warehouse and trucks
-
Dock lips that create a positive stop
-
Bumpers to prevent damage
-
Wheel chocks to halt vehicle movement
With a typical loading dock leveler having a capacity range from 25,000 to 80,000 lbs, it’s evident that loading docks are designed to handle substantial loads, streamlining the material handling process.
Loading Bay
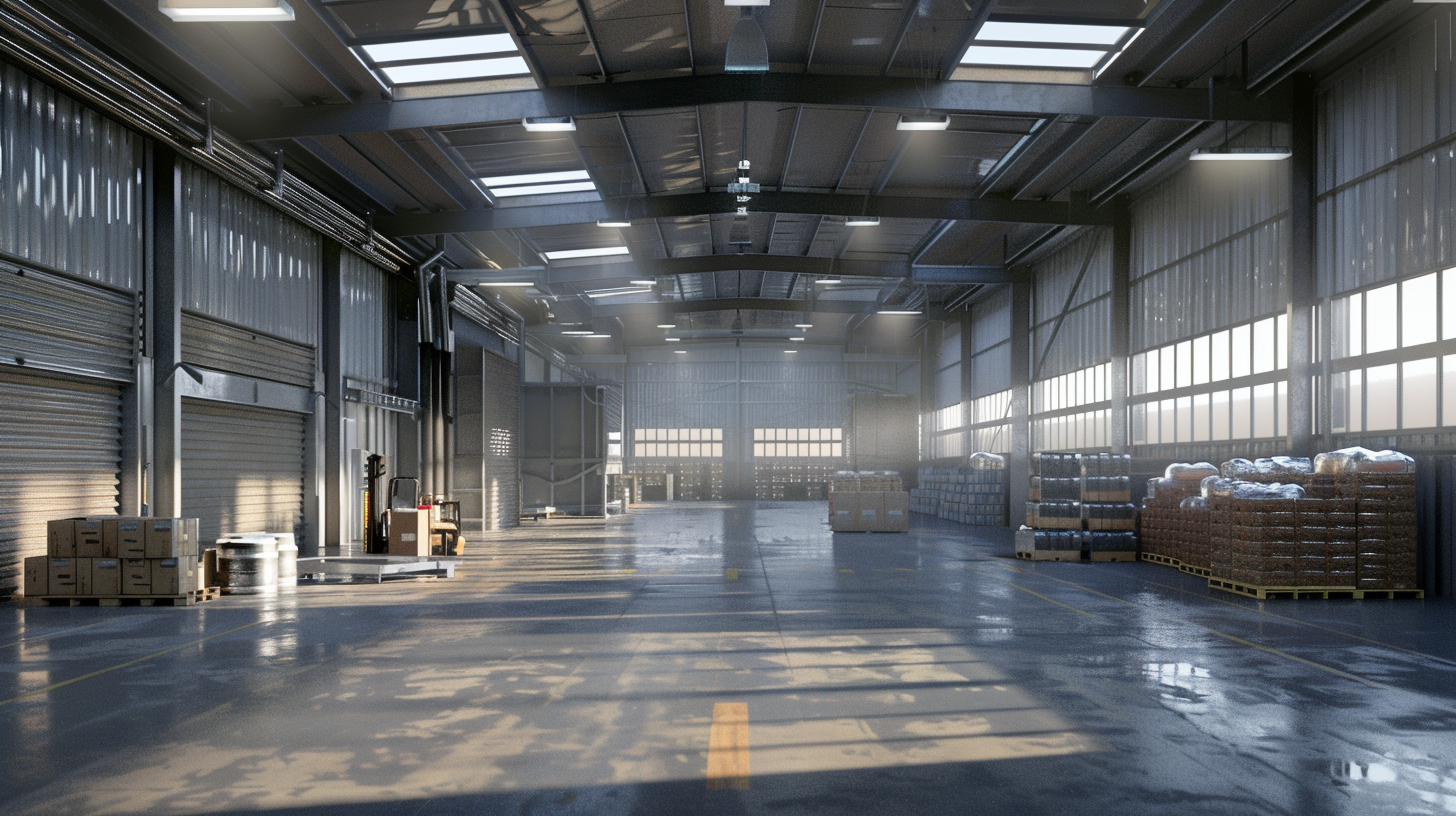
If a loading dock is the gateway, a loading bay is the pathway. It’s an area within a building where goods and materials are loaded and unloaded from vehicles. These versatile zones are commonly found in warehouses, factories, and other commercial facilities, often tucked away at the rear of the building to facilitate the loading and unloading process.
The design of loading bays can vary, with some being level with the vehicle bed, while others have height differentials to match various truck heights. This height differential, the difference between the highest truck height and the dock height, is a key consideration in the design of loading bays. It allows them to flexibly accommodate different vehicle sizes, making them a versatile solution in logistics operations.
Key Differences Between Loading Docks and Loading Bays
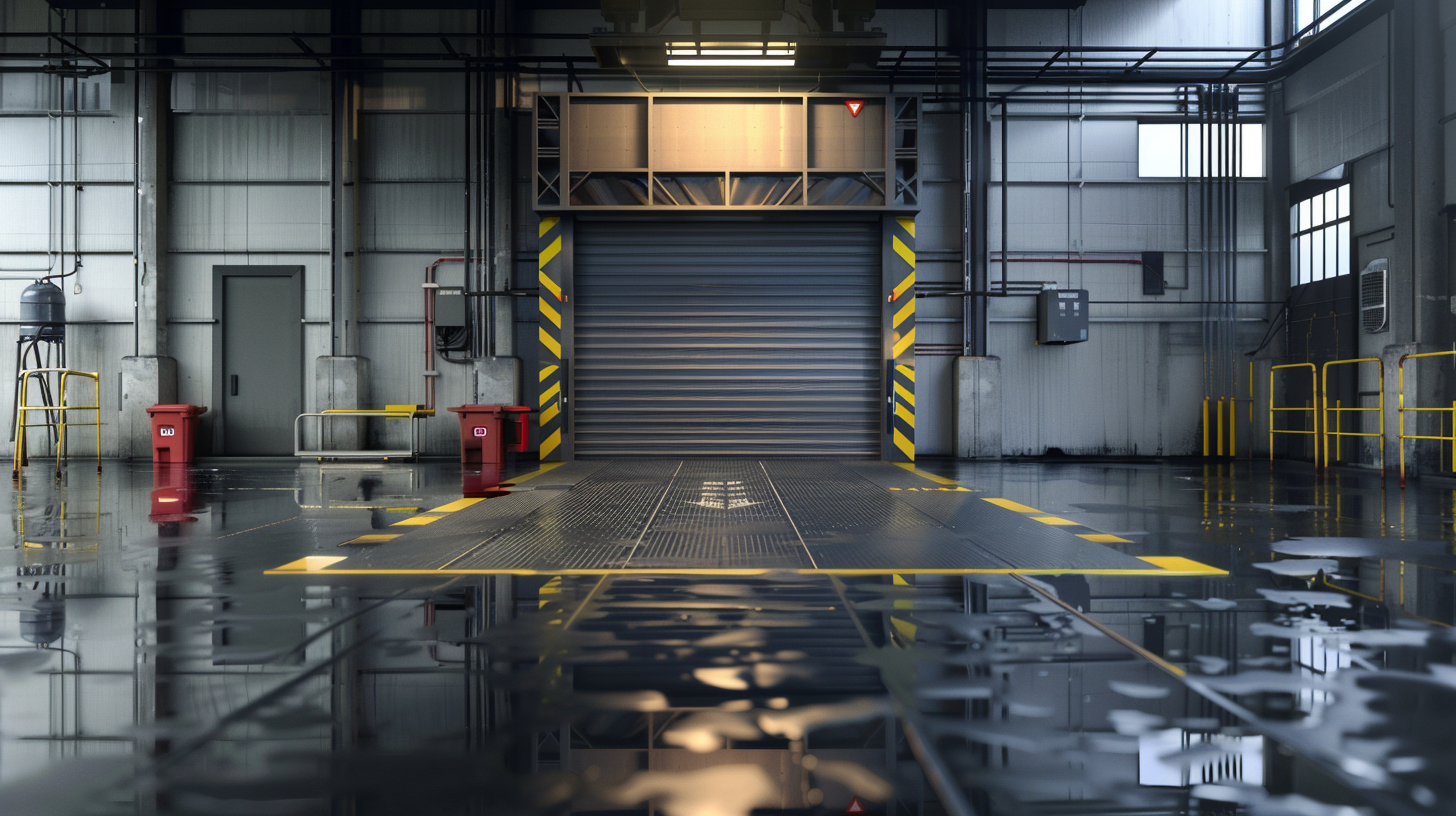
Despite their shared role in facilitating the handling of goods, loading docks and loading bays are not identical twins. They each possess unique characteristics that set them apart.
Loading docks are specific elevated platforms used for unloading trucks, facilitating a direct access point for loading and unloading. In contrast, loading bays, while performing the same functions, are more versatile. They offer additional space for staging, moving, and storing goods, thereby providing better management of goods within the warehouse.
This additional space makes loading bays a more comprehensive solution, contrasting with the singular purpose of loading docks for direct loading and unloading tasks.
Design and Structure
The most striking difference between loading docks and loading bays lies in their design and structure. Loading bays are the chameleons of the logistics world. They offer adaptability in design to accommodate a range of vehicle sizes and shapes for various loading and unloading scenarios. Their layout and design are pivotal in optimizing space utilization, enhancing traffic flow, and supporting efficient docking equipment use within warehouse operations.
On the other hand, loading docks are specialized platforms, often elevated, that align with the height of truck trailers to facilitate smooth loading and unloading processes. Their elevations are typically fixed at around 48 inches in the United States to match the common truck trailer height. The selection of the appropriate type of loading dock door, from high-speed, rolling, sectional, to knockout doors, is also crucial in warehouse operations. Safety barriers, such as guard chains or bars, must also be installed to prevent falls from docks with a drop of four feet or more.
Functionality and Efficiency
The functionality and efficiency of loading docks and loading bays also differ. Loading docks are well-equipped with dock levelers and dock lifts that bridge the gap between the dock and the truck, accommodating various vehicle sizes, and enhancing loading and unloading processes. They also employ advanced technology, like high-speed dock doors and automated dock doors, enhancing safety and operational efficiency.
In contrast, loading bays may lack some of these specialized equipment. Operational efficiency and safety at loading bays may be compromised without specialized equipment like dock levelers or vehicle restraints, which are common at loading docks. While loading bays offer versatility in space utilization and can operate both indoors and outdoors, their efficiencies may be hindered when they lack elevation or certain features to streamline operations.
Usage Scenarios
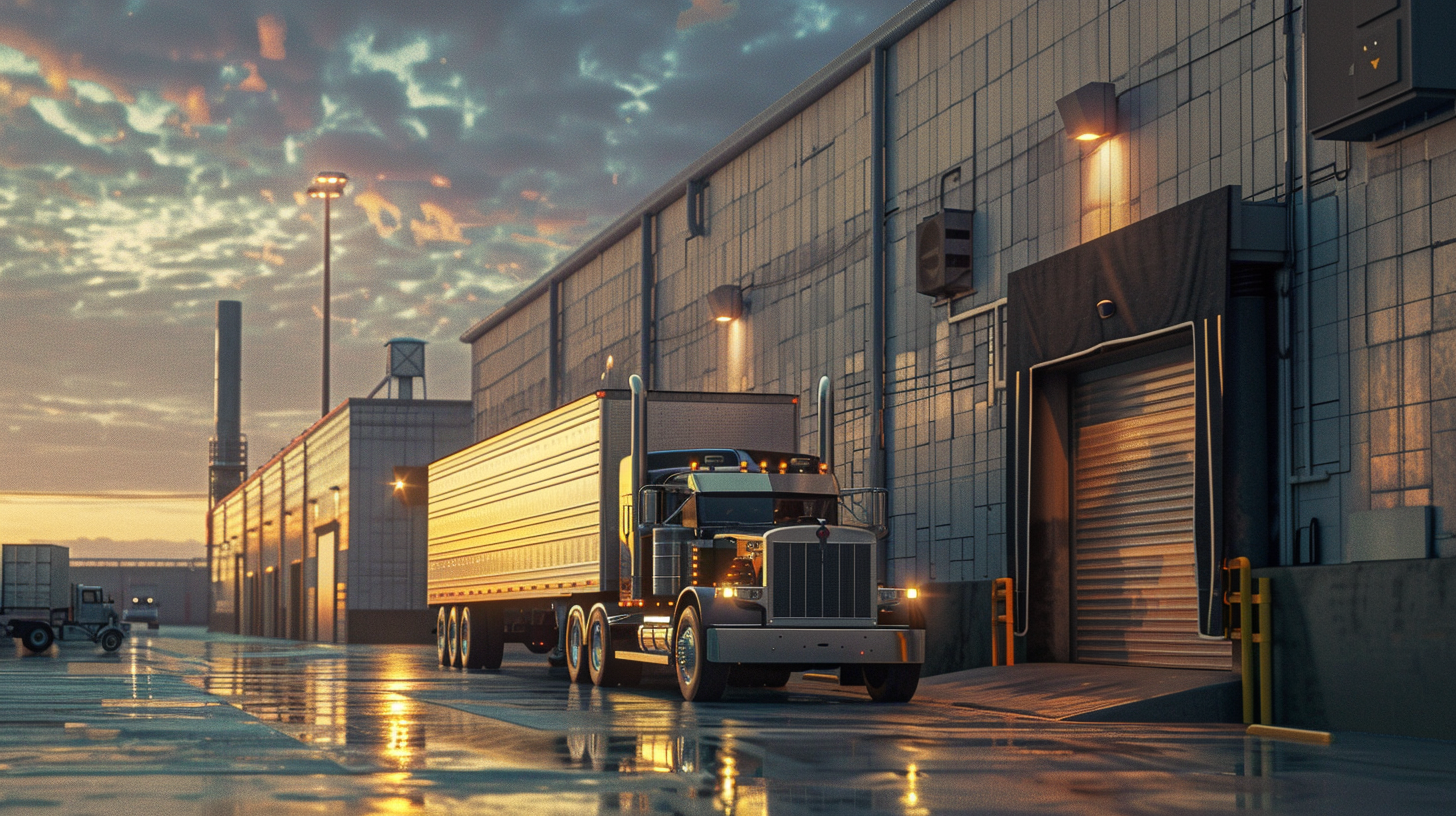
The choice between a loading dock and a loading bay often comes down to the specific usage scenarios of a warehouse. Loading docks are typically preferred for high-volume warehouses with a constant stream of shipments, requiring efficient and safe handling of goods.
Loading bays offer versatility and are suitable for:
-
Warehouses that require adaptability for various activities
-
Warehouses where temporary setups are needed
-
Smaller facilities or retail stores lacking a dedicated dock
Loading bays provide a viable solution for the movement of goods.
Advantages and Disadvantages of Loading Docks and Loading Bays
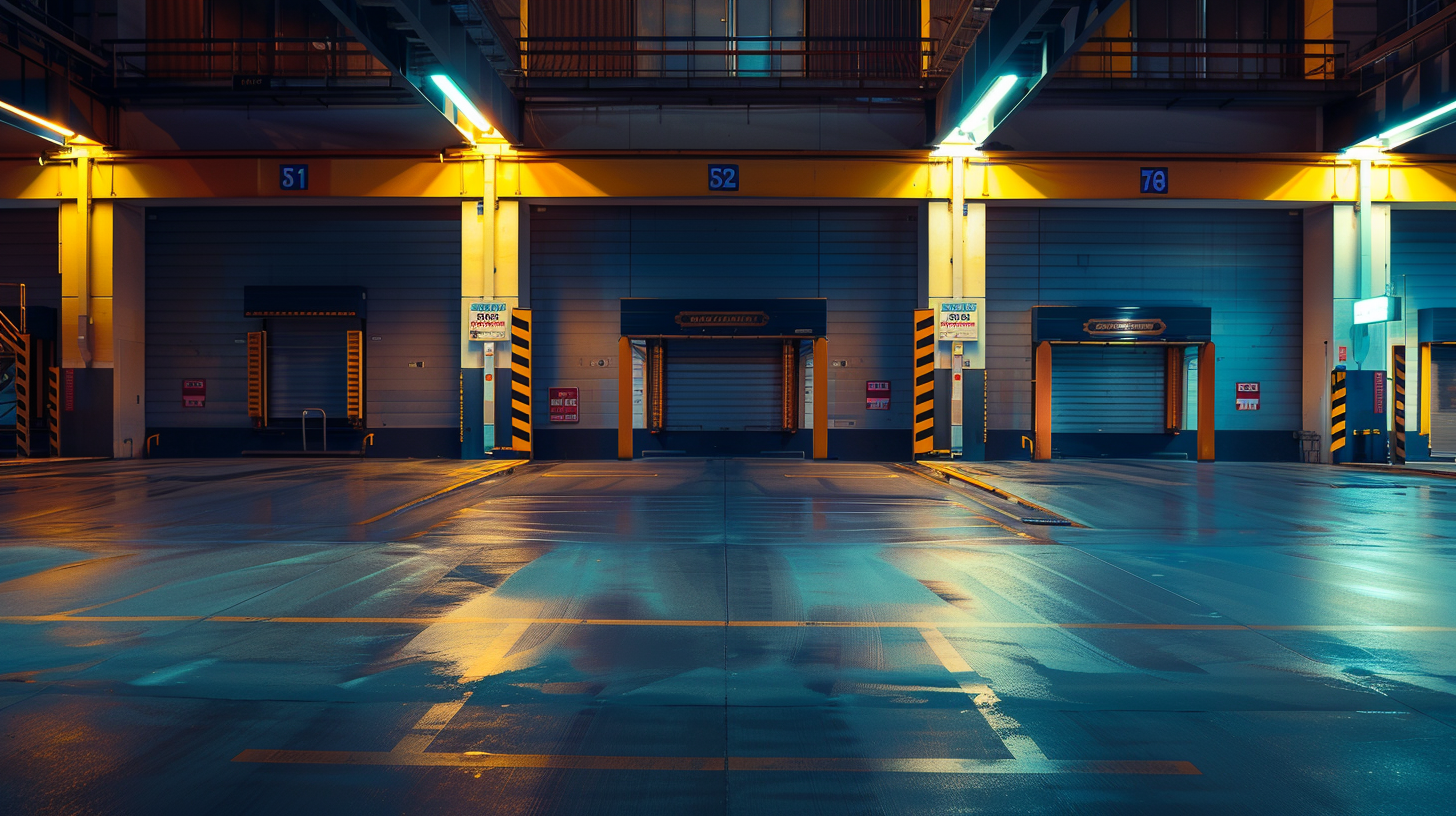
Like any other infrastructure, loading docks and loading bays come with their set of advantages and disadvantages. These revolve around factors such as efficiency, space utilization, and safety considerations. Let’s delve into each of these and assess their pros and cons.
Pros of Loading Docks
The key advantages are:
-
Maximizing the flow of goods in and out of the warehouse
-
Ensuring quick and efficient service to customers
-
Offering security and insulation with low maintenance
-
Being suitable for larger industrial spaces
The design of loading docks, with features like sectional dock doors, contributes to these advantages.
Dock levelers are a significant component of loading docks, bridging the gap between the trailer and warehouse, suitable for weight capacities typically ranging from 25,000 to 80,000 lbs. The use of this and other specialized equipment, like hydraulic dock levelers and vehicle restraints, improves safety and operational efficiency by bridging gaps and preventing vehicle movement during loading.
Moreover, the use of automated truck loading systems (ATLS) at loading docks can expedite the transfer of goods from conveyors to trucks, offering a safe and efficient transport and installation process.
Cons of Loading Docks
Despite the numerous advantages, loading docks are not without their drawbacks. They are the site of approximately 25% of accidents in the industrial sector. In fact, between 2017 and 2019, there were a total of 71 accidents reported at loading docks according to OSHA. This has led to a growing concern about the declining loading dock safety in the industry.
Certain designs of loading docks, like sawtooth loading docks, have poor space utilization due to their design, which is intended to manage limited outdoor maneuvering space. Open loading docks face challenges related to weather exposure, theft risk, and inadequate protection for products and workers. Additionally, the cost of installing loading docks, which includes platforms and safety equipment, can range from $50,000 to $100,000, with additional maintenance costs.
Pros of Loading Bays
Loading bays, on the other hand, boast several advantages. They facilitate the direct transfer of goods from the warehouse to the truck, minimizing travel distances and potential delays. The installation of loading bays can lead to cost savings by reducing the reliance on manual labor and optimizing workforce utilization.
The design of loading bays can enhance:
-
Security and protection against weather
-
Efficiency of operations
-
Supply chain management
-
Customer satisfaction through better inventory tracking and synchronized transportation schedules.
Cons of Loading Bays
However, loading bays are not perfect either. They can suffer from energy inefficiency due to energy loss through doors, which can be mitigated with dock seals and shelters. Exposure to the elements at loading bays can lead to damage of goods and create hazardous working conditions, necessitating the use of dock shelters and mats for safety.
Functional considerations for loading bays include the need for adjustable lighting, suitable exterior doors, and mitigation of noise exposure to ensure a well-operating facility. Loading bays without proper vehicle restraint systems risk incidents such as driveaways or trailer creep, adding to the 7% of forklift accidents caused by trucks moving away from docks. Moreover, the lack of weather protection at loading bays can increase the risk of slips, trips, and falls due to slippery surfaces, especially if seals or shelters are not installed around dock doors.
Choosing the Right Solution for Your Warehouse
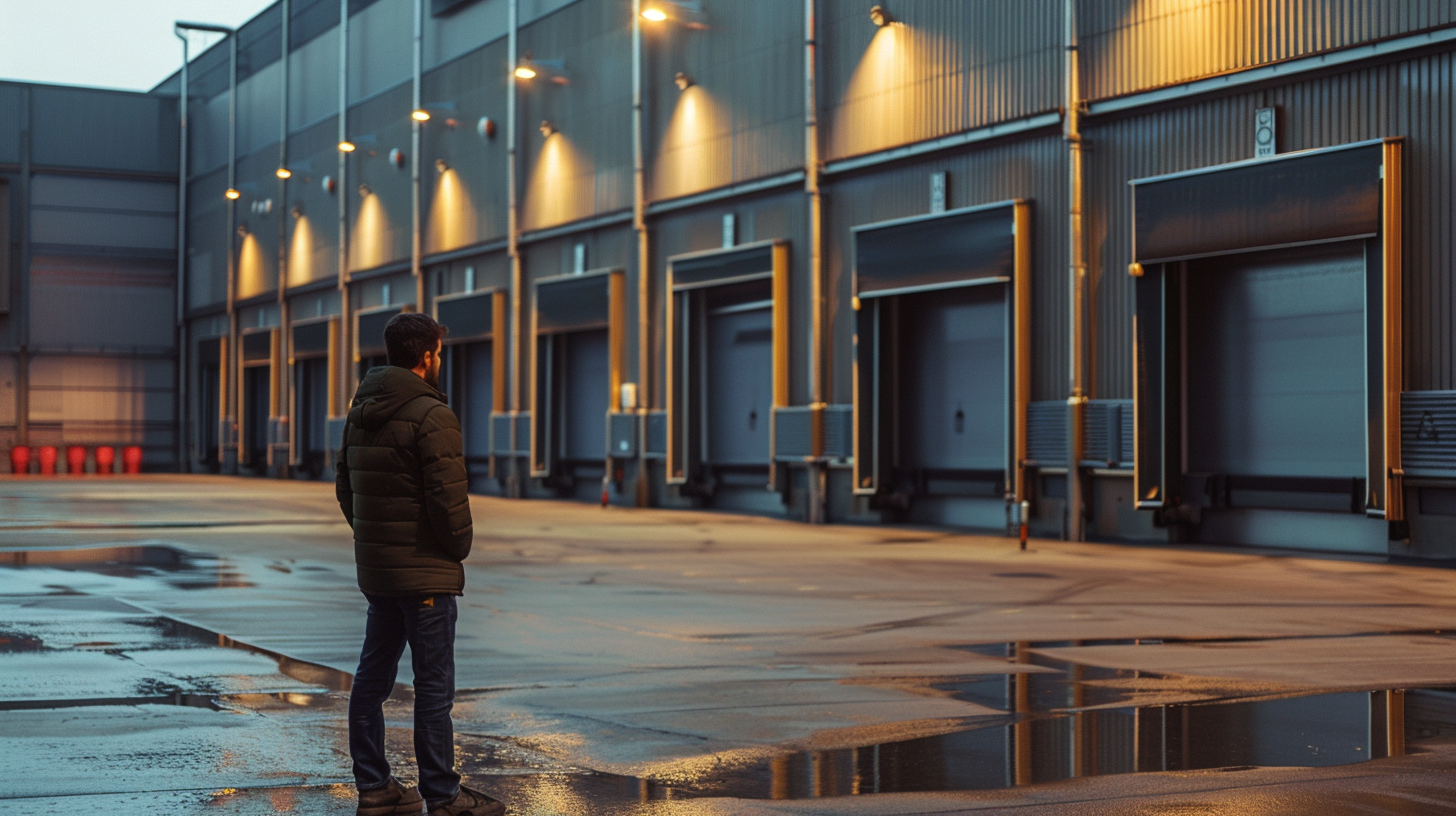
When it comes to selecting the right solution for your warehouse, there’s no one-size-fits-all answer. The choice between a loading dock and a loading bay depends largely on your specific needs, including space requirements, the type of goods being handled, and future adaptability.
Let’s explore some factors to consider when choosing the right solution for your warehouse.
Factors to Consider
When choosing a loading solution, there are several factors to consider:
-
Efficiency: Warehouse loading docks and doors should be efficient to ensure smooth and timely movement of goods.
-
Security: Loading docks and doors should be secure to prevent theft and unauthorized access.
-
Reliability: The loading dock system should be reliable to minimize downtime and delays in operations.
-
Ease of operation: The loading dock system should be easy to operate to ensure smooth and efficient loading and unloading of goods.
-
Adaptability: The loading dock system should be adaptable to accommodate future changes in business operations, such as different types of vehicles or changes in shipping and receiving processes.
Considering these factors will help you choose the right loading solution for your warehouse.
Another important factor to consider is energy efficiency. Opt for energy-efficient loading dock systems with features like insulated doors and weather seals to reduce energy consumption and operational costs.
Customizing Your Loading Solution
Customization is key to ensuring that your loading solution meets your specific needs. Modular Loading Dock Platforms, for example, can be quickly installed, accommodating warehouses with time or budget constraints. They can be utilized in leased or temporary settings without permanent alterations.
Loading dock doors can be customized to meet the specific needs of a warehouse, with options such as lightweight rolling doors, low-maintenance sectional doors, and fast-operating high-speed doors.
Additionally, dock management can be optimized through the use of software solutions like myQ that offer detailed monitoring, alert systems for equipment issues, and scheduling software to streamline loading operations.
Safety and Maintenance Considerations
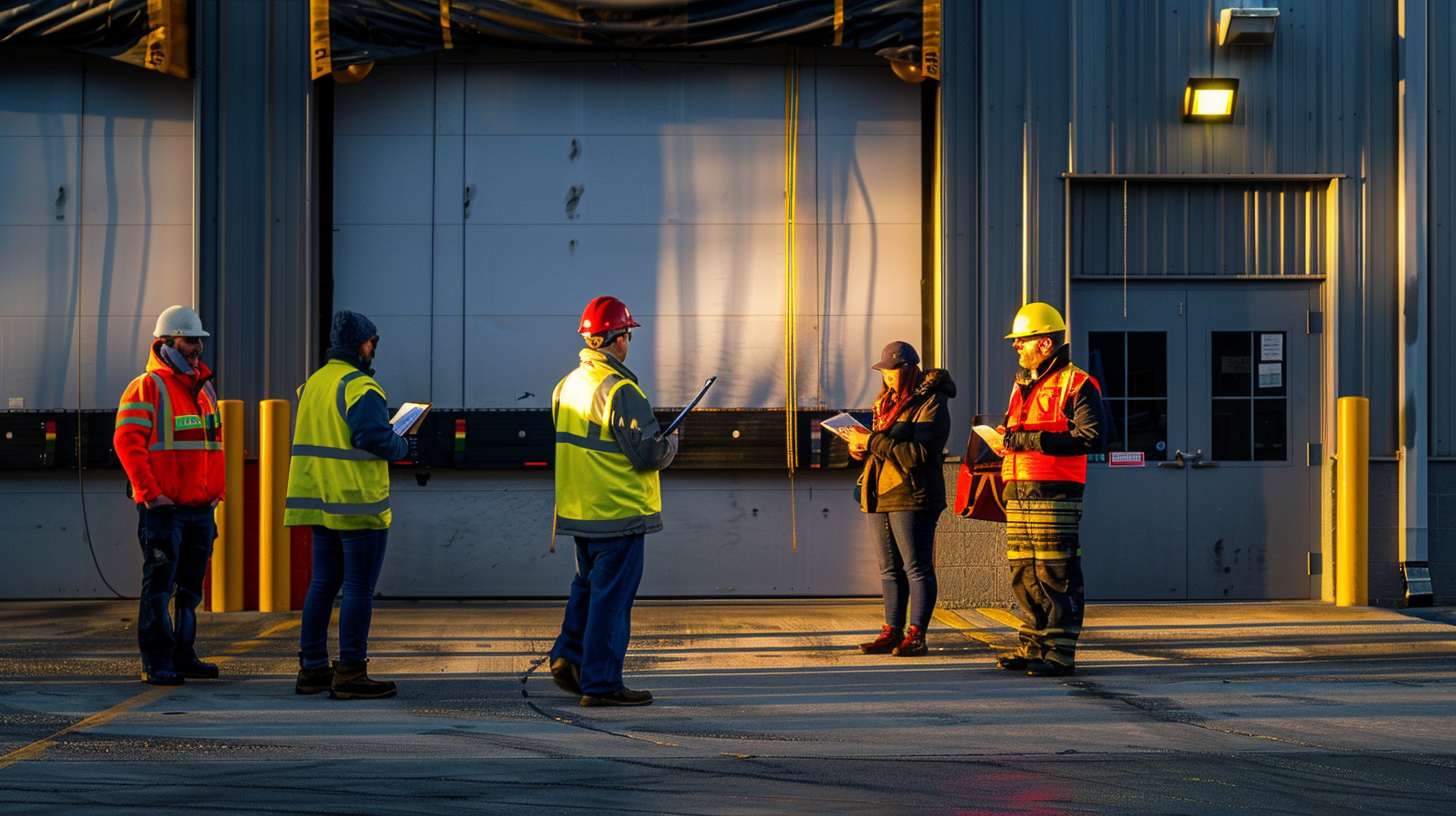
Safety and maintenance are two critical considerations when it comes to loading docks and bays. Proper lighting in and around the dock area is crucial for safe operation, helping loading dock operating personnel load and unload inventory safely, and alerting pedestrians about the loading and unloading zone.
Workers in loading docks, including truck drivers, are at risk of inhaling dangerous chemicals, suffering from dehydration, or experiencing discomfort, highlighting the need for adequate safety measures.
Safety Precautions
Safety precautions are a must for any loading solution. These include implementing safety measures such as:
-
Trailer locks
-
Safety barriers
-
Proper lighting
-
Audible alarms
-
Vehicle restraints
-
Dock lights
-
Indicator systems
Training employees thoroughly on safety practices is also crucial to prevent accidents and improve efficiency.
Furthermore, it’s important to maintain a clean and safe working environment. Here are some essential steps in maintaining safety at the loading docks and bays:
-
Regular cleaning
-
Keeping floors and dock plates dry
-
Addressing hazards like laceration risks immediately
-
Installing barriers to prevent accidents and falls
Maintenance Tips
Finally, maintenance plays a vital role in ensuring the longevity and safety of your loading dock or bay. Conducting regular inspections and timely repairs of loading dock equipment, such as levelers, seals, and shelters, is crucial for their proper and safe functionality.
Implementing daily cleaning schedules and routine pressure washing helps maintain a safe and clean work environment by preventing the accumulation of debris and minimizing hazards at loading docks. To minimize damage, heavy-duty rubber dock bumpers should be used, and any damage to storage racks must be reported and repaired promptly.
Summary
In conclusion, both loading docks and loading bays play pivotal roles in warehouse operations. Their unique characteristics, advantages, and drawbacks make them suitable for different scenarios and requirements.
Whether you choose a loading dock or a loading bay depends largely on your specific needs, including the type of goods being handled, the space available, and future adaptability. Always prioritize safety, efficiency, and regular maintenance when choosing and operating your loading solution.
Frequently Asked Questions
What is a bay at a loading dock?
A loading bay is a designated area in warehouses and industrial buildings for loading and unloading goods, while a loading dock refers to the actual platform to which a truck or other vehicle connects to in order to unload.
What is a truck dock called?
A truck dock is called a loading dock, which is a staging platform for loading or unloading shipments. It is commonly found on commercial and industrial buildings, including warehouses.
What is the purpose of loading dock?
The purpose of a loading dock is to provide a designated area for loading and unloading goods from trucks and vans, typically found in commercial and industrial buildings, warehouses, and distribution centers. It serves as the arrival and departure point for large shipments, offering a space for staging, supervision, and organization of incoming and outgoing items.
What are some safety precautions for loading docks and loading bays?
To ensure safety at loading docks and bays, it's crucial to implement measures like trailer locks, safety barriers, proper lighting, vehicle restraints, and provide thorough safety training for employees. Taking these precautions can significantly reduce the risk of accidents and injuries.
Owner, Parts Brite
My background is in Electrical and Software Engineering, but since I started PartsBrite.com in 2016, I've focused on everything related to docks.
My team and I are here to help those looking to repair or replace their dock levelers, bumpers, door, and door lights.
1-855-PartsBrite | partsbrite.com | paul@partsbrite.com
Leave a comment