Efficient Loading: The 3 Purposes of A Dock Leveler Spring
Springs are an essential part of dock levelers, optimizing tension and allowing adjustment to various trailer heights. This brief introduction will explore why do dock levelers use springs, conveying their fundamental role in making loading tasks smoother and safer.
Key Takeaways
-
Springs in dock levelers are crucial for the lifting mechanism, enabling precise height adjustments and providing cushioning during loading operations, which accommodates vehicles of different heights and ensures a safer loading process.
-
Dock levelers require regular maintenance and replacement of springs, which are vital components for operation. Inspecting springs for wear, adjusting tension, and replacing damaged springs are essential for efficient and safe dock leveler performance.
-
Choosing the right dock leveler involves considering factors such as vehicle types, usage frequency, load capacity, safety, and maintenance needs. Mechanical dock levelers rely on springs, while hydraulic levelers offer an alternative with fewer maintenance demands.
The Role of Springs in Dock Levelers
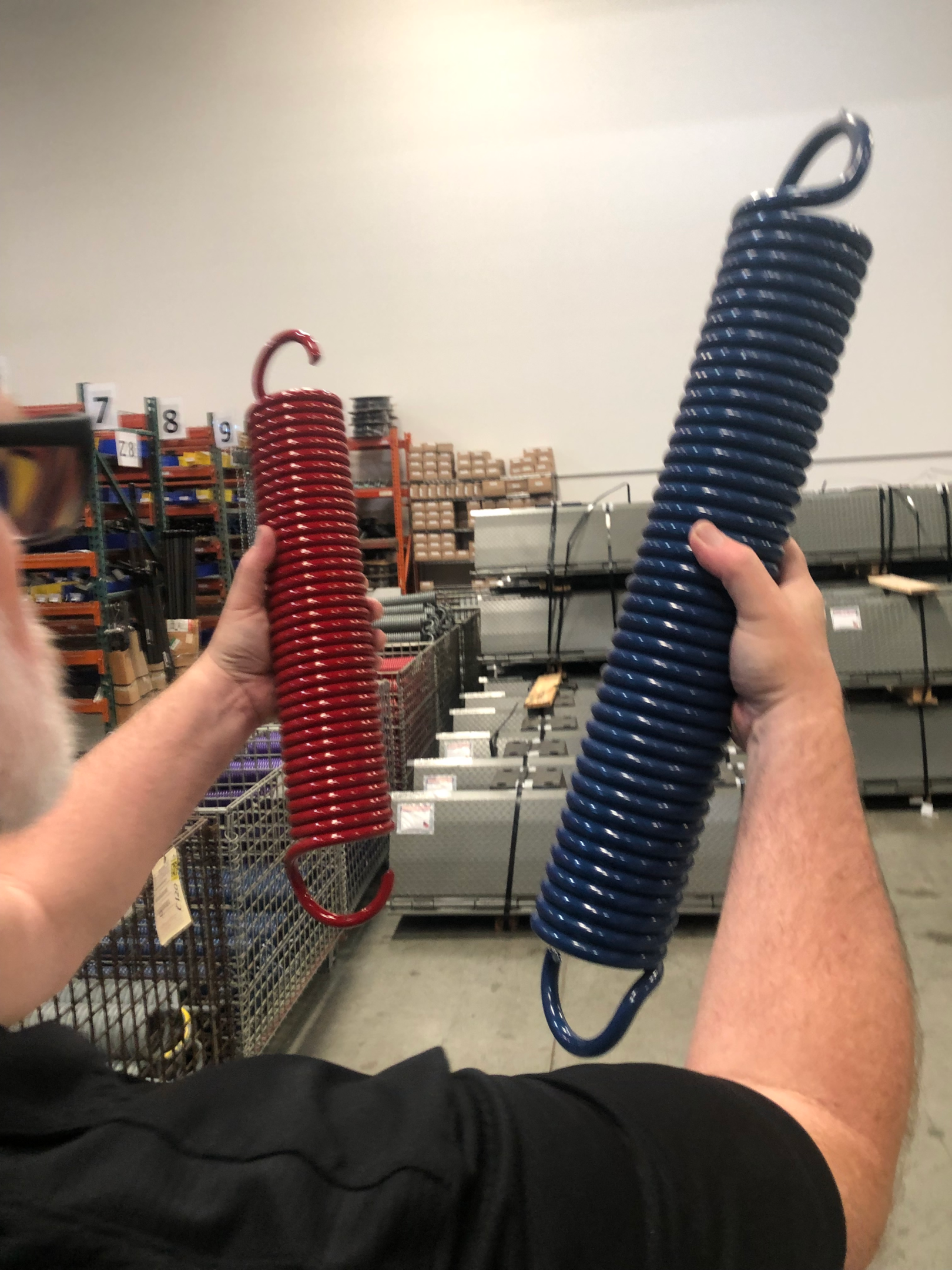
Springs in dock levelers are more than just coiled metal. They form the backbone of these machines, providing the necessary tension to keep the dock leveler in place and maintain a consistent level for the leveler’s deck. They cushion the impact when the dock leveler is in use, protecting the equipment and facilitating smoother operations during loading and unloading.
But the springs’ function doesn’t end there. They are the unsung heroes that accommodate vehicles of various heights, allowing for precise height adjustment and a safer loading process in the dock pit. Moreover, they release and allow the dock leveler to descend slowly and in a controlled manner when activated, thus preventing accidental lowering and ensuring the proper use of the dock plate.
The role of springs in dock levelers is complex and multifaceted. Whether it’s a hydraulic dock leveler or a mechanical one, springs ensure the smooth functioning of these machines and contribute to the seamless operations of loading docks.
Lifting Mechanism
Springs play a crucial role in the lifting mechanism of dock levelers. They provide the necessary force to lift the leveler deck and lip into position, thereby aiding in height adjustment. So, how does this mechanism work?
Dock levelers use two types of springs for lifting: extension springs and compression springs. Extension springs extend as the leveler is lowered and compress to lift the platform, aiding in height adjustment. On the other hand, compression springs compress as the deck lowers, then exert a pushing force to elevate the platform. This intricate interplay between the two types of springs ensures the smooth operation of the lifting mechanism.
Counterbalance System
The counterbalance system forms another essential part of dock levelers, ensuring smooth and controlled movement during operation. A dock leveler spring keeps the leveler in the ‘stored’ position when not in use, enabling the leveler to descend when activated.
Springs within the dock leveler are calibrated to manage the substantial weight sustained by the levelers during the loading and unloading process. The system also incorporates mechanical safety legs to prevent the dock leveler from dropping more than 4 inches below dock level if the truck unexpectedly departs. Snubbing springs aid in raising the leveler’s lip, providing a cushion that assists in extending the dock leveler lip to connect with the truck floor. All of these mechanisms work together to ensure a safe and efficient loading process.
Types of Springs Used in Dock Levelers
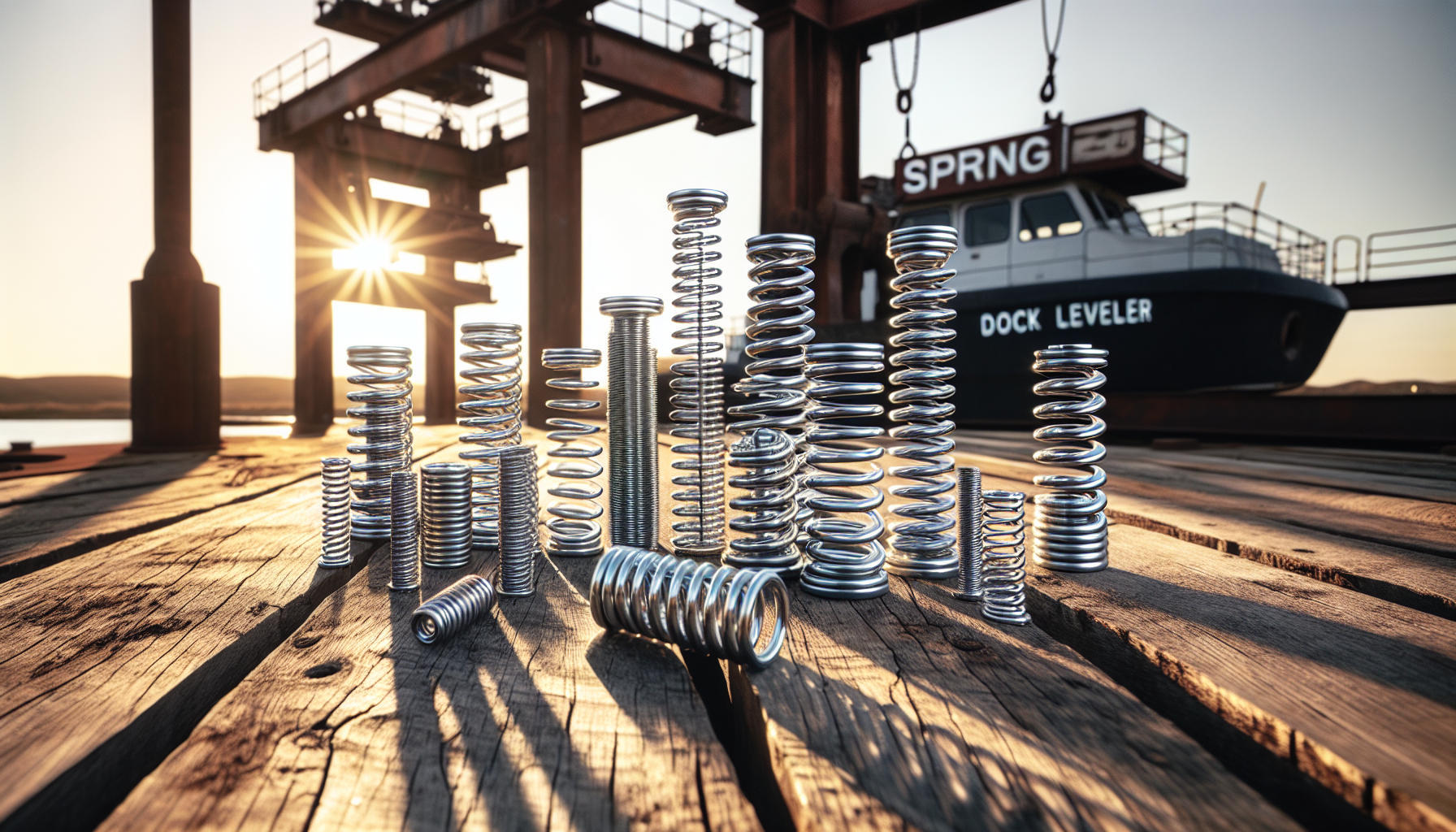
With springs playing such a crucial role in dock levelers, it’s important to understand the types of springs that these machines utilize. Dock levelers typically use three kinds of springs: extension springs, compression springs, and snubbing springs. Each of these springs serves a specific function and contributes to the efficient operation of the dock levelers.
Snubber springs and lip extension springs, for instance, serve essential functions in air-powered and hydraulic dock levelers to ensure their correct operation. Understanding these springs’ roles can help in maintaining the dock levelers and ensuring their long-term performance.
Compression Springs
Compression springs are a key component in dock levelers. These springs can store energy and release it as needed to lift the leveling platform. Their ability to maintain performance over many cycles contributes to the long lifespan of the dock leveler.
The solid construction of compression springs provides strength and durability, allowing them to handle high-stress applications like dock levelers. Moreover, compression springs require minimal maintenance, making them suitable for use in dock levelers where ease of maintenance is a valuable feature.
Extension Springs
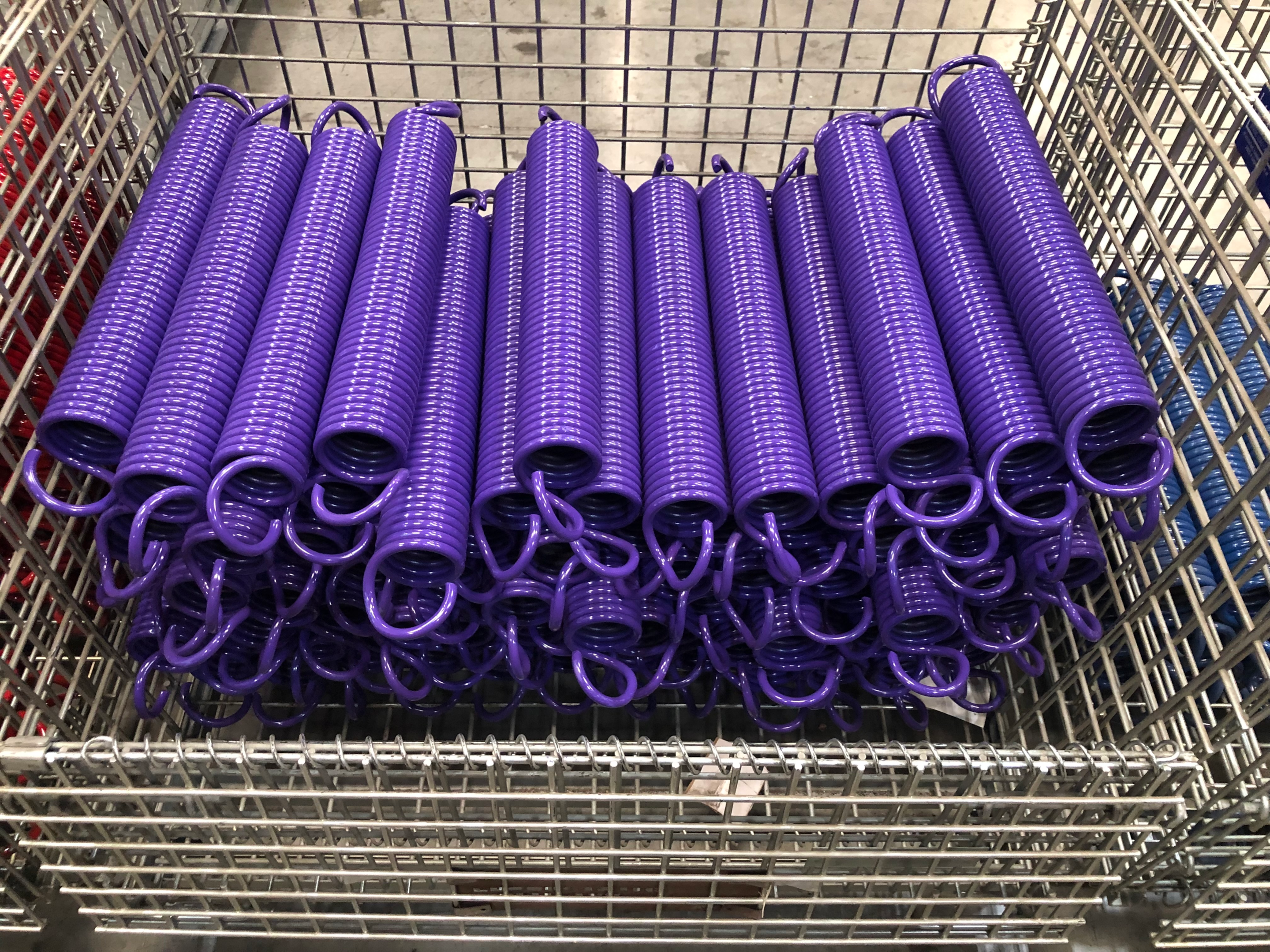
Similarly, extension springs play a key role in dock levelers. They extend as the leveler is lowered and compress to counterbalance the weight of the platform during lifting. This action is integral to the height adjustment mechanism in dock levelers.
The main advantage of extension springs is their ability to:
-
Store energy
-
Exert a pulling force
-
Operate with a tension load
-
Stretch as the load is applied to them
This is necessary for the controlled ascent and descent of the pit leveler platform and for the height adjustment process in dock levelers.
Maintenance and Replacement of Dock Leveler Springs
Dock leveler springs, like any other mechanical components, require regular maintenance and inspection to ensure optimal performance and safety. Their role in positioning the dock leveler lip makes regular inspections crucial. Moreover, maintenance over time is essential to ensure continued efficient operation of dock levelers.
A well-maintained spring can prevent long-term damage and allows for issues to be rectified before they escalate. However, maintenance costs, including repair costs, are significant in the total cost of ownership, making it important to consider factors such as the accessibility of components and frequency of required maintenance.
Inspecting Springs for Wear and Damage
Inspecting dock leveler springs should be a routine activity. It involves checking for signs of wear or damage such as:
-
rust
-
deformation
-
decreased elasticity
-
breaks
Regular inspection is essential to identify issues that may compromise the efficiency or safety of the dock leveler.
Dock leveler springs should be inspected at least once a month to catch any early signs of rusting, fraying, or breaks. When signs of wear or damage are observed, prompt replacement is necessary to ensure the safety and efficiency of the dock leveler.
Adjusting Spring Tension
Adjusting spring tension is another crucial aspect of dock leveler maintenance. It is essential to handle different weights and heights of loads or trailers effectively. Here’s how to adjust spring tension:
-
Use a wrench to modify the tightness of the spring adjustment nut.
-
Turn the nut clockwise to increase the spring tension.
-
Turn the nut counterclockwise to decrease the spring tension.
Once the springs are installed or adjusted, testing the dock leveler for correct functionality ensures smooth operation. This process helps maintain the optimal tension in the springs, allowing the dock leveler to function efficiently under various loading scenarios.
Replacing Worn or Damaged Springs
Despite regular maintenance and inspections, springs can wear out or get damaged over time. The spring is the most commonly repaired part of dock leveler equipment, highlighting its importance to dock leveler function. A qualified technician should conduct inspections of the spring mechanisms every 90 days to discover signs of wear or damage that warrant replacement.
The replacement process involves using lifting equipment, such as a crane or forklift, to safely handle the heavy components. It is important to adhere to the specific guidelines set forth by the manufacturer, as replacement procedures vary with different types of dock levelers.
Hydraulic vs. Mechanical Dock Levelers: The Use of Springs
While springs play an integral role in mechanical dock levelers, it’s important to note that not all dock levelers rely on springs. Hydraulic dock levelers, for instance, do not have wearable parts such as springs, reducing maintenance needs associated with such components. On the other hand, mechanical loading dock levelers operate using springs which assist in lifting and lowering the leveler deck.
Choosing between hydraulic and mechanical dock levelers depends on various factors such as the frequency of use, load capacity, and maintenance considerations. Both types have their own merits and drawbacks, and understanding the role of springs in each of these types can help in making an informed choice.
Springs in Mechanical Dock Levelers
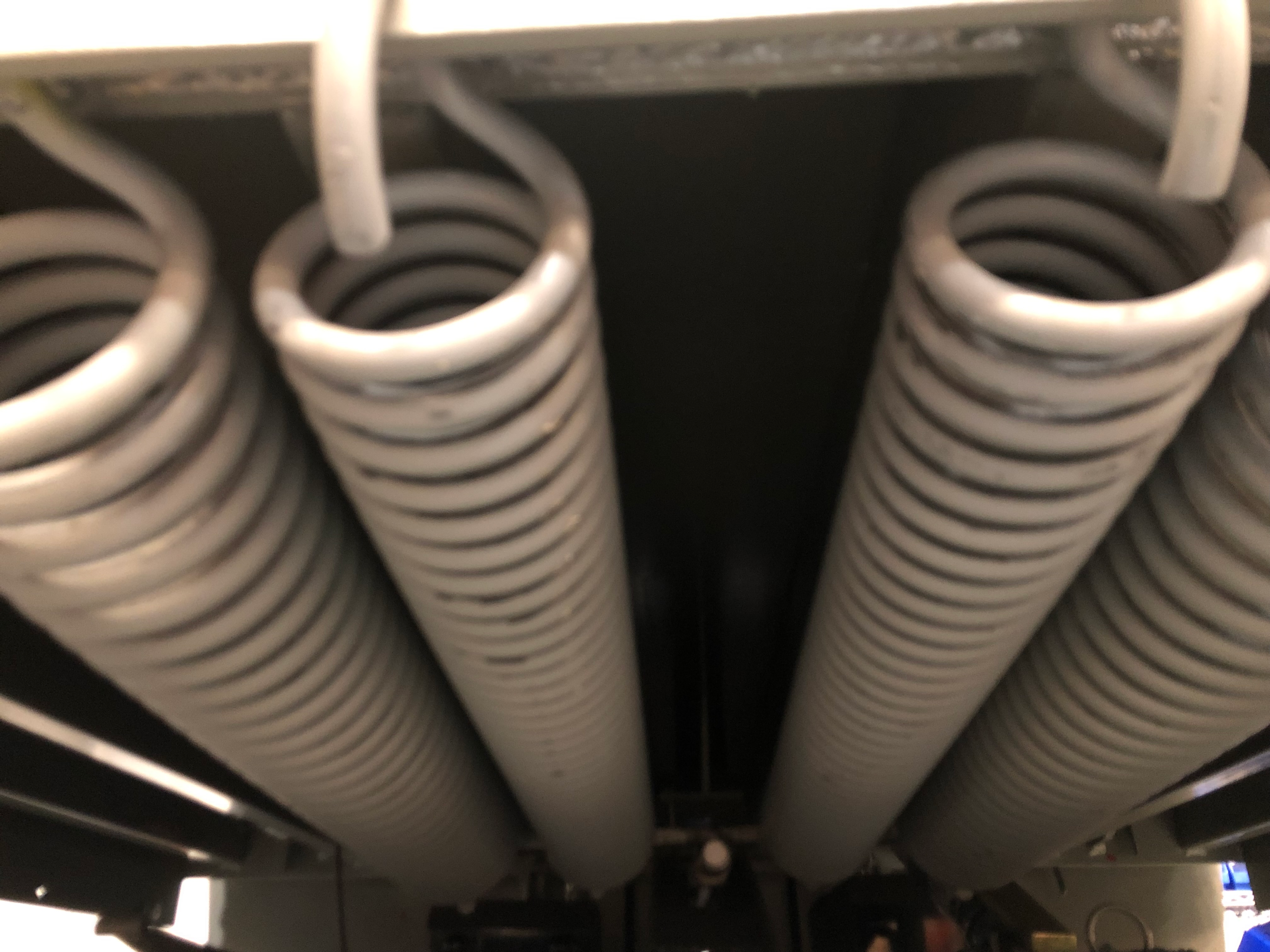
In mechanical dock levelers, loading dock leveler springs play a vital role. They are activated by a releasable holdown device and can be released by pulling a release chain, allowing the mechanical dock leveler to adjust to various truck heights.
The main extension springs are crucial for the functioning of mechanical dock levelers, as they are the primary components enabling the lifting and lowering actions. This makes the mechanical dock levelers versatile in handling various loading scenarios.
Hydraulic Dock Levelers: An Alternative
On the other hand, hydraulic dock levelers offer a different functioning mechanism. They use hydraulic cylinders and a hydraulic pump to automatically lift and place the leveler and lip, offering smooth and consistent operation.
Designed to handle heavier loads and more frequent usage, hydraulic levelers are well-suited for facilities with high-volume operations. With fewer moving parts than mechanical systems, hydraulic dock levelers typically require less maintenance than a mechanical leveler, leading to significant long-term cost savings. Moreover, the control panel on a hydraulic leveler facilitates easy operation, with push-button controls simplifying the process and improving efficiency and safety during operation.
Safety Considerations for Dock Levelers with Springs
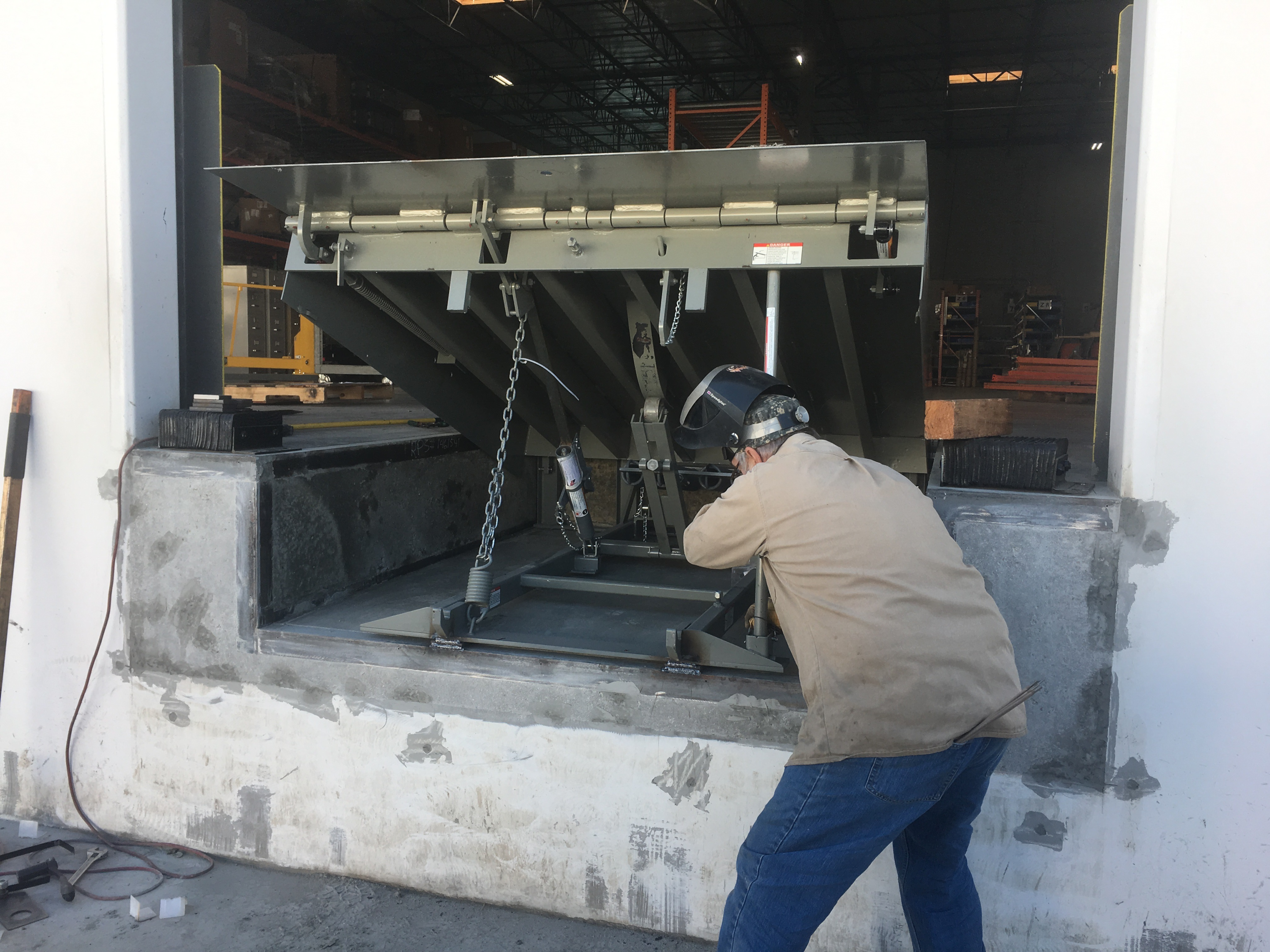
Safety is paramount in any operation, and dock levelers are no exception. Proper spring tension and regular maintenance are essential for dock leveler safety. The dock edge should be painted a reflective yellow to improve visibility and reduce the risk of accidents.
It’s important to remember that regular maintenance, correct tensioning, and timely replacement of dock leveler springs are critical to preventing injuries or damage to equipment. Daily inspections of dock levelers are key to ensuring that emergency equipment is readily accessible and that there are adequate protections against vacant dock drop-offs and free-fall hazards.
Proper Spring Tension
Proper spring tension is a crucial safety aspect in dock levelers. Improper tension can prevent proper descent or cause the leveler to descend too quickly, potentially leading to equipment damage or personal injury.
Correct spring tension is vital to ensure that the dock leveler is securely held in place and to provide cushioning during the impact of loading and unloading. Routine adjustments of spring tension are essential to maintain the controlled lowering and optimal performance of dock leveler operations.
Regular Maintenance and Inspection
Regular inspections and maintenance are essential for dock leveler safety. Failure to maintain dock levelers regularly could result in serious injuries or fatalities, as well as damage to the dock and trucks. Ensuring compliance with current OSHA regulations is another important aspect of maintenance.
The counterbalance system in dock levelers, which includes mechanical safety legs, prevents the ramp from falling more than 4 inches below dock level in case of sudden truck departure. Additional safety features, such as guarding or safety lips, can prevent accidental falls when a bay door is left open and stop vehicles from rolling off the dock platform.
Choosing the Right Dock Leveler for Your Facility
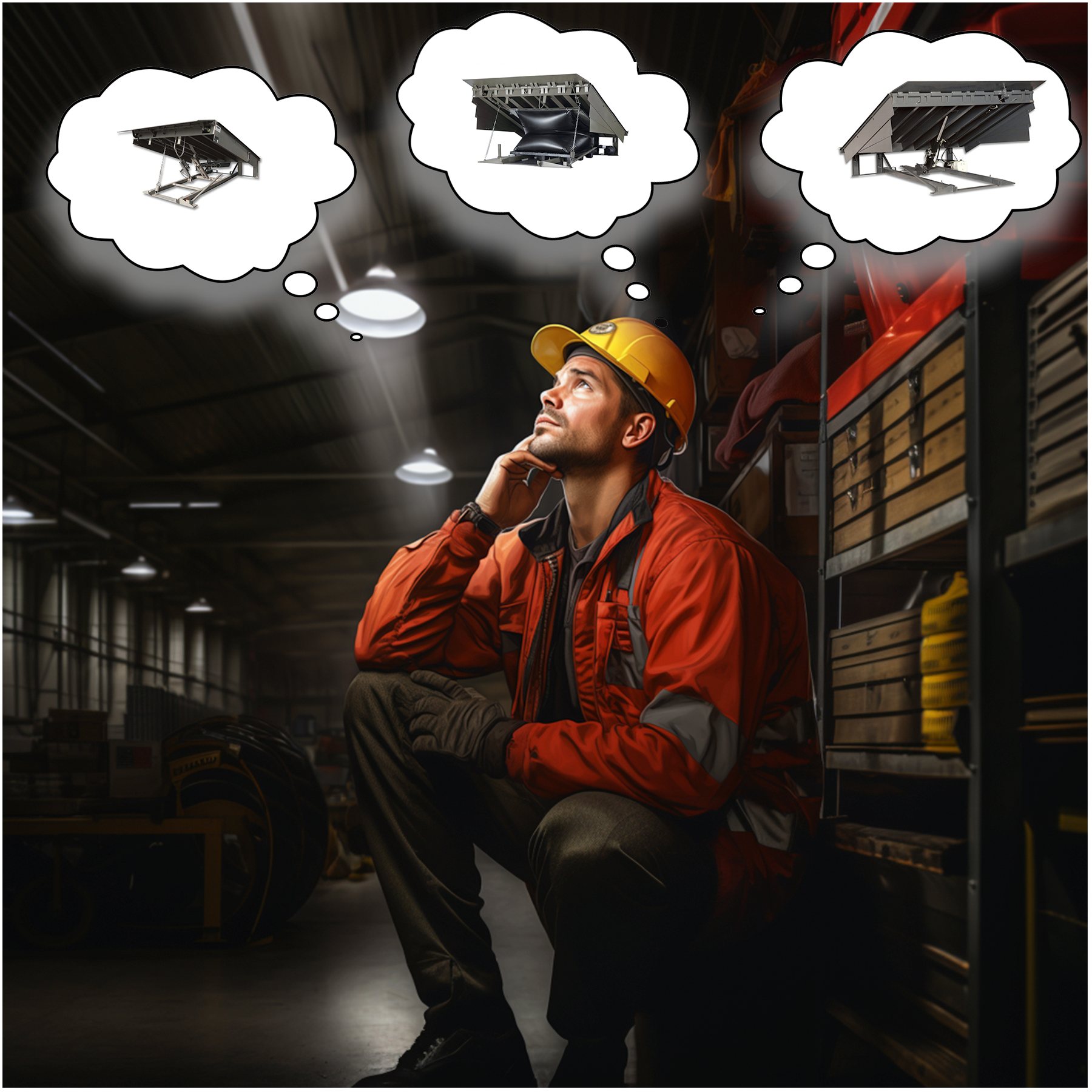
Choosing the right dock leveler for your facility requires careful consideration. Factors to consider include:
-
The types of vehicles that use the dock
-
Trailer dimensions
-
Frequency of use
-
Load capacities
-
Future growth
Balancing cost with capability, ensuring long-term safety, and choosing credible manufacturers and dealers for reliable service and support are also crucial.
There are manual and air powered dock levelers to choose from, including the loading dock leveler. Manual levelers are fitting for docks with low traffic with no need for electricity, while powered levelers are better for high-traffic docks, accommodating a range of trailer heights and ease of operation under various dock scenarios. The choice of dock leveler should also accommodate environmental considerations, such as insulation or wash-down capabilities.
Assessing Your Loading Dock Needs
When assessing your loading dock needs, it’s important to consider the weight capacity. The weight capacity of dock levelers typically ranges from 25,000 to 80,000 pounds, covering the needs of over 90% of applications. To estimate the needed capacity of a dock leveler, add the weight of the forklift and the heaviest load it carries, and then multiply the total by 2.5.
Specialized requirements, such as hygiene standards in certain industries, must also be taken into account. This may call for specific types of dock levelers like vertical mounted or edge of dock levelers.
Comparing Dock Leveler Options
Finally, when choosing a dock leveler, it’s important to compare the options available. Dock levelers come in three basic types: hydraulic, mechanical, and power-assisted mechanical units, each catering to specific operational requirements. It is crucial to select dock levelers that match the load and lift truck specifications to prevent overloading and equipment failure.
For operations with lighter loads and minimal trailer height variation, Edge of Dock (EOD) levelers are a cost-effective solution. Powered levelers, on the other hand, offer benefits in maintenance, safety, and productivity over manual levelers. Edge of Dock Levelers and Dock Lifts can also deviate from standard dock height considerations, adapting to varied operational needs and height adjustment requirements.
Summary
In conclusion, dock levelers are pivotal in ensuring efficient loading and unloading operations in logistics. Springs play a critical role in their functioning, facilitating lifting mechanisms, counterbalancing weights, and ensuring safety. Regular maintenance, inspection, and timely replacement of these springs are crucial for the optimal performance and safety of dock levelers. Whether you choose a hydraulic or mechanical dock leveler, understanding the role of springs and their maintenance requirements can greatly enhance the lifespan and efficiency of your dock leveler. So, the next time you see a dock leveler in action, take a moment to appreciate the humble springs that keep the wheels of logistics turning smoothly.
Frequently Asked Questions
What is the mechanism of dock leveler?
A dock leveler uses a pull chain activation to raise the deck, then can be easily lowered back down to the bed of a trailer or to a stored position using an extended range hold-down mechanism. This mechanism ensures smooth operation and control of the lip during use.
Should dock levelers should always be kept elevated?
Dock levelers should always be kept elevated to avoid hazards for forklifts driving across the dock. Always train employees to return levelers to their normal stored position after use.
What are the disadvantages of dock leveler?
The disadvantages of mechanical dock levelers include an increased potential for repetitive-use injuries to loading dock personnel and inefficiency in facilities with high loading dock traffic. These factors should be considered when choosing dock leveler options.
What is the life expectancy of a dock leveler?
The life expectancy of a hydraulic dock leveler is a minimum of ten years, after which it may need replacement due to issues such as motor failure or welding damage.
Why are springs important in dock levelers?
Springs are essential in dock levelers as they provide tension to keep the leveler in place, cushion impacts, accommodate vehicles of different heights, and enable controlled descent. Their importance lies in ensuring the functionality and safety of the dock leveler.
Owner, Parts Brite
My background is in Electrical and Software Engineering, but since I started PartsBrite.com in 2016, I've focused on everything related to docks.
My team and I are here to help those looking to repair or replace their dock levelers, bumpers, door, and door lights.
1-855-PartsBrite | partsbrite.com | paul@partsbrite.com
Leave a comment